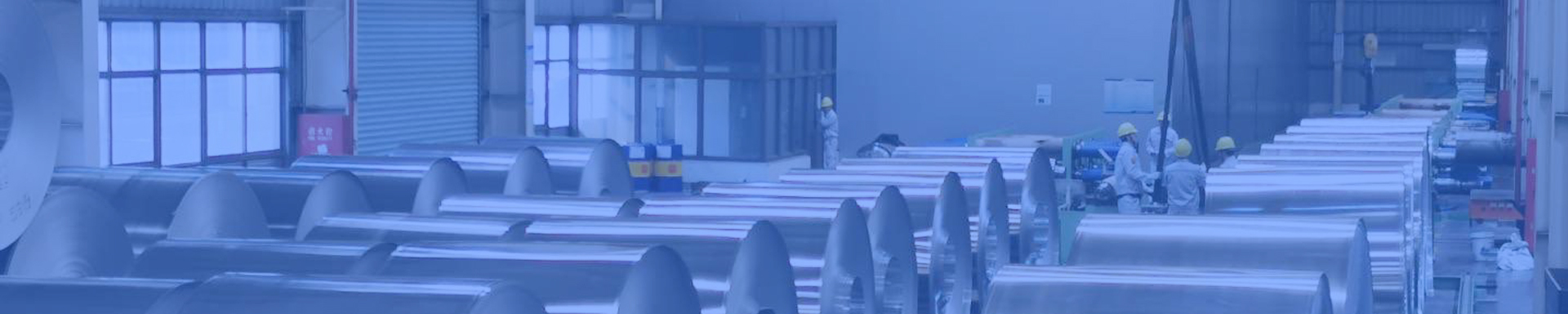
Kepala Kon Penggelek Keluli tuang
Kepala kon penggelek keluli pemutus ketepatan GW jika salah satu komponen penting kilang penggelek.
- GW Precision
- Luoyang, China
- Penetapan Kontrak
- 1000 keping
- maklumat
Casting Steel Roller Cone Head
The casting steel roller cone head is mainly used in metallurgical rolling mills, mining machinery, heavy equipment and other occasions that require high radial and axial loads. Its design feature is the use of tapered roller bearings (such as TIMKEN series) to simultaneously withstand radial and axial forces, suitable for high impact, high speed or heavy load conditions.
Application scenarios of casting steel roller cone head
1. Main application areas
Hot/Cold Rolling Mill: Supports the working roll, intermediate roll, or support roll to withstand rolling force and axial movement.
Mining machinery: used for transmission systems of heavy equipment such as crushers and ball mills.
Wind power equipment: large wind turbine main shaft bearing seat.
Ships/heavy machinery: high load rotating components such as propeller shafts and gearboxes.
2. Job characteristics
High load: withstands radial force (rolling force) and axial force (rolling roll movement).
High temperature/high pollution environment: Heat resistance and oxidation prevention are required under hot rolling conditions; The mining environment needs to be dust-proof and waterproof.
High precision requirement: The fitting accuracy between the inner hole of the bearing seat and the outer ring of the bearing (usually H7 or H8 level).
Heat treatment process for conical bearing seat of cast steel roller
The conical bearing seat of the cast steel roller is usually made of low-alloy cast steel (such as ZG35CrMo, ZG42CrMo), and the heat treatment process is as follows:
1. Pre treatment (annealing or normalizing)
Purpose: To eliminate casting stress, refine grain size, and improve machinability.
Process: Heat to 850-900 ℃ and keep warm before air cooling (normalizing) or furnace cooling (annealing).
2. Quenching and tempering treatment (quenching+tempering)
Quenching: Heat to 850-900 ℃ (depending on the material), oil quenching or water quenching (to prevent deformation).
Tempering: Tempering at 500-650 ℃ to obtain a martensitic structure, balancing strength and toughness (hardness HB 250-320).
3. Local surface strengthening (optional)
Induction hardening: High frequency quenching of the bearing installation surface to improve wear resistance (hardness HRC 50-55).
Carburizing/nitriding: suitable for high alloy steel to enhance fatigue resistance.
4. Stress relief annealing (after precision machining)
Low temperature annealing at 200-300 ℃ eliminates machining stress and prevents deformation.
Function introduction:
1. Transmission of torque: Cone heads are used to transmit the rotational torque of the motor more
efficiently, ensuring a smooth rolling process.
2. Improve connection stability: The cone head design helps to improve the connection stability between
the roller head and the coupling shaft, reducing loosening or wear at high speeds.
3. Adaptation to different rolling needs: The design of the cone head helps to adapt to different types of
rolling processes, such as hot rolling and cold rolling, as well as the rolling needs of different materials.
Related Products